Hoe te ûntwerpen plestik dielen
Koarte beskriuwing:
Nei ûntwerp plestik ûnderdielenis om de foarm, grutte en presysiteit fan 'e dielen te definiearjen, basearre op' e rol dy't de dielen yn it produkt spielje, en de regel fan it foarmproses foar it plestik. De definitive útfier is tekeningen foar de fabrikaazje fan skimmel en it plestik diel.
Produktfabryk begjint mei ûntwerp. It ûntwerp fan plestik ûnderdielen bepaalt direkt it realisearjen fan 'e ynterne struktuer, kosten en funksje fan it produkt, en bepaalt ek de folgjende stap fan skimmelproduksje, kosten en syklus, lykas it ynjeksjefoarmjen en postferwurkingsproses en kosten.
Plastike ûnderdielen wurde breed brûkt yn ferskate produkten, foarsjennings en libbens fan minsken yn moderne maatskippij. Plestik ûnderdielen fereaskje ferskillende foarmen en funksjes. Se brûke plestik materialen en har eigenskippen binne farieare. Tagelyk binne d'r in protte manieren om plestik dielen yn 'e sektor te meitsjen. Dus om plestik ûnderdielen te ûntwerpen is gjin ienfâldige taak.
Ferskillende dielûntwerp en materiaal wurde ferskate ferwurking produsearre. De ferwurking foar it foarmjen fan plestik omfettet benammen hjirûnder:
1. ynjeksje foarme
2. waait foarmjen
3. kompresjefoarmjen
4. rotaasjefoarmjen
5.thermfoarming
6. ekstrúzje
7. fabrikaazje
8.foaming
D'r binne ferskate manieren om se massaal te produsearjen. Injeksjefoarmjen is populêre produksjemetoade, om't ynjeksjefoarm 50% ~ 60% plestik ûnderdielen wurde produsearre troch injeksjefoarm, it is in produksje-fermogen mei hege snelheid.
Lit saak sjen foar guon plestik ûnderdielen dy't wy ûntwurpen:
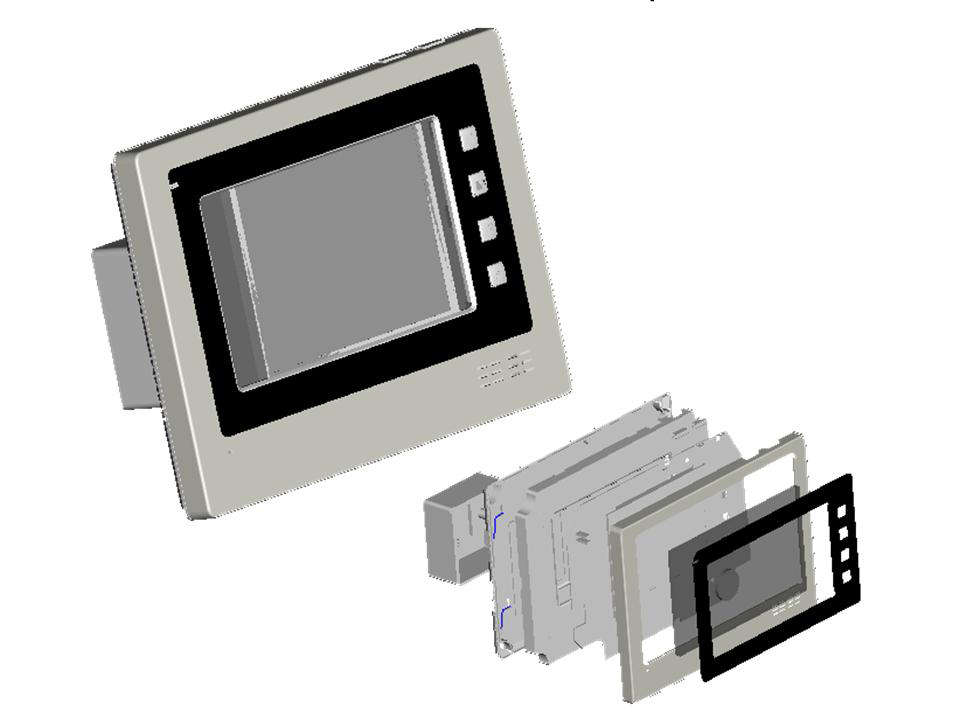
Plestik behuizing fan fisy tillefoan
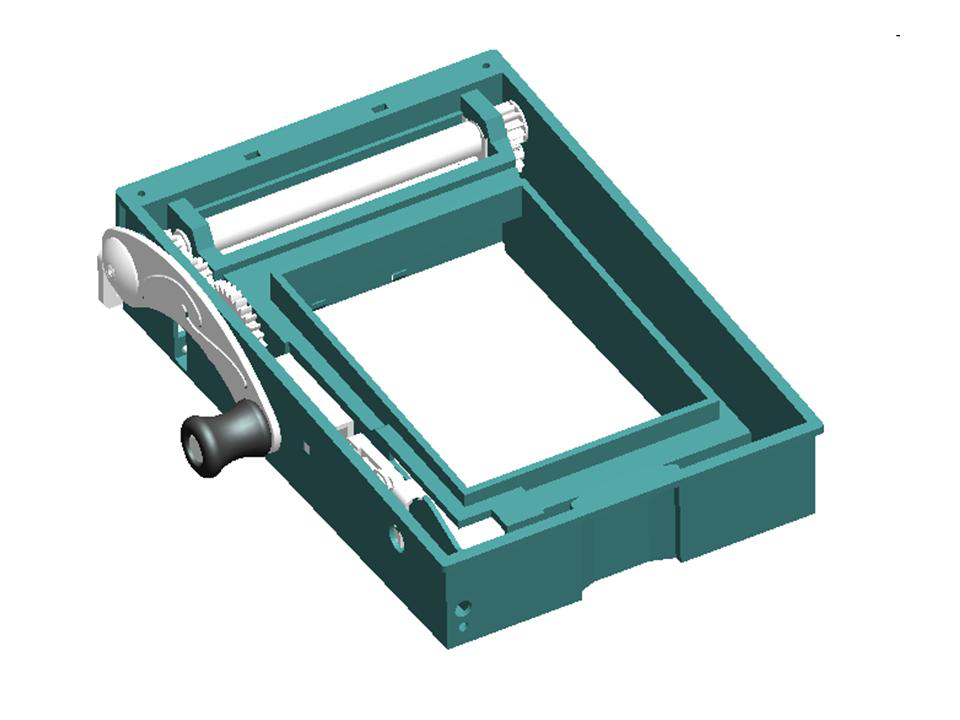
Plestik dielen fan meganisme
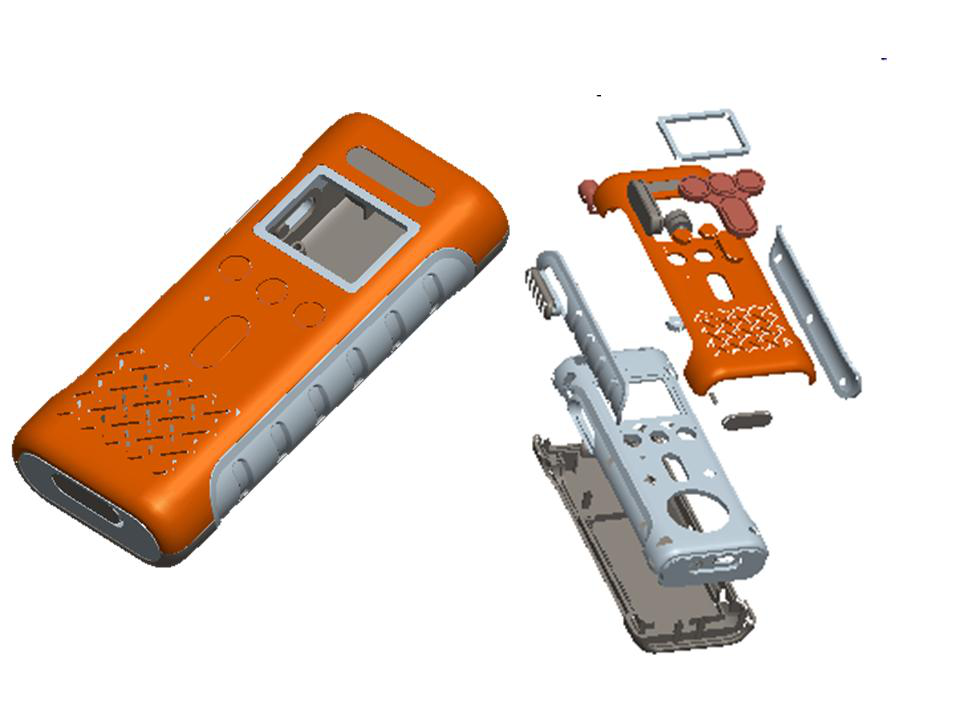
Plestik gefallen fan elektroanyske
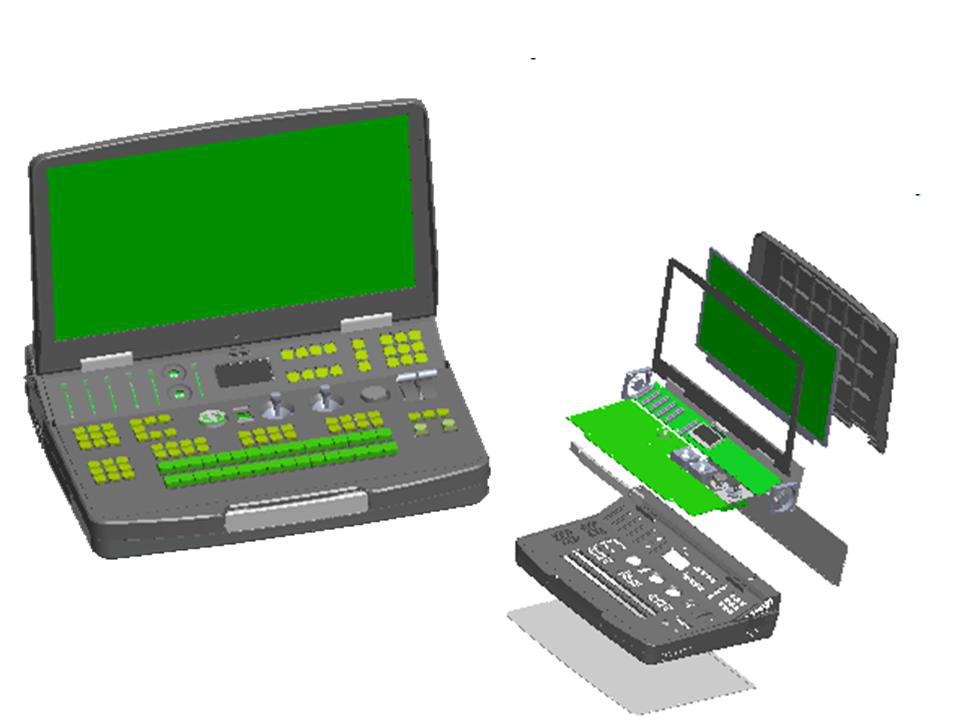
Plestik húsfesting foar ynstrumint
Hjirûnder diele wy detail hoe't jo plastic dielen yn trije aspekten kinne ûntwerpe
* 10 tips foar ûntwerp fan plestik dielen dy't jo moatte wite
1. Bepale it ûntwerp en de grutte fan it produkt.
Dit is de earste stap yn it heule ûntwerpproses. Neffens merkûndersyk en klanteasken bepale it uterlik en de funksje fan produkten, en formulearje taken foar produktûntwikkeling.
Neffens de ûntwikkelingstaak draacht it ûntwikkelteam de technyske en technologyske helberensanalyse nei it produkt, en bout it 3D-uterlikmodel fan it produkt. Dan wurde neffens funksjesrealisaasje en produktassemblage mooglike ûnderdielen pland.
2. Skieden yndividuele dielen fan produkttekeningen, kies plestik harstype foar plestik dielen
Dizze stap is om de dielen te skieden fan it 3D-model dat yn 'e foarige stap is krigen en se as yndividueel te ûntwerpen. Neffens de funksjonele easken fan 'e ûnderdielen, kieze geskikte plestik grûnstoffen as hardwarematerialen. ABS wurdt bygelyks normaal brûkt yn 'e
shell, ABS / BC as PC is ferplicht om beskate meganyske eigenskippen te hawwen, transparante ûnderdielen lykas lampekap, lampepost PMMA as PC, gear- of wearedielen POM as Nylon.
Nei it selektearjen fan it materiaal fan 'e dielen kin it detailûntwerp begon wurde.
3. Definearje konsepthoeken
Untwerp hoeken kinne it plestik út 'e mal ferwiderje. Sûnder trekhoeken soe it diel wichtige wjerstân oanbiede fanwegen wriuwing by ferwidering. Untwerp hoeken moatte oanwêzich wêze oan 'e binnen- en bûtenkant fan it diel. Hoe djipper it diel, hoe grutter de konsepthoek. In ienfâldige regel is om in konsepthoek fan 1 graden per inch te hawwen. Net genôch trekwinkel kin resultearje yn skuorren lâns de kanten fan it diel en / as grutte markearders fan ejectorpen (mear hjirop letter).
Untwerphoeken fan bûtenflak: Hoe djipper it diel, hoe grutter de trekhoek. In ienfâldige regel is om in konsepthoek fan 1 graden per inch te hawwen. Net genôch trekwinkel kin resultearje yn skuorren lâns de kanten fan it diel en / as grutte markearders fan ejectorpen (mear hjirop letter).
Normaal wurdt tekstuer makke op it oerflak fan dielen om goed uterlik te hawwen. De muorre mei tekstuer is rûch, wriuwing is grut, en it is net maklik om it út 'e holte te heljen, dus it is in gruttere tekenhoek nedich. De grovere tekstuer is, de gruttere tekenhoek is nedich.
4. Definearje wanddikte / unifoarme dikte
Fêste foarmfoarming is net winske yn ynjeksjefoarming fanwegen folgjende redenen:
1) .Koaltiid is proporsjoneel oan fjouwerkant fan muurdikte. Lange koeltiid foar solid sil de ekonomy fan massaproduksje ferslaan. (minne geleider fan waarmte)
2) .Dikere seksje krimpt mear dan tinner seksje, yntrodusearret dêrtroch differinsjele krimp dy't resulteart yn warpage of sinkmark ensfh. (Krimpkarakteristiken fan keunststoffen en pvT-skaaimerken)
Dêrom hawwe wy basisregel foar ûntwerp fan plestik diel; sa fier mooglik muorndikte moat troch it diel unifoarm of konstant wêze. Dizze wanddikte hjit nominale wanddikte.
As der in solide seksje yn it diel is, dan moat it hol wurde makke troch kearn yn te fieren. Dit moat soargje foar unifoarme wanddikte om 'e kearn.
3) .Wat binne de oerwagings foar it besluten fan muurdikte?
It moat dik en stiif genôch wêze foar de baan. Wanddikte kin 0,5 oant 5 mm wêze.
It moat ek dun genôch wêze om rapper te koelen, wêrtroch legere dielgewicht en hegere produktiviteit is.
Elke fariaasje yn wanddikte moat sa min mooglik wurde hâlden.
In plestik diel mei wikseljende muurdikte sil ferskille koelingssifers en ferskillende krimp ûnderfine. Yn sa'n gefal wurdt it berikken fan nauwe tolerânsje heul dreech en in protte kearen ûnmooglik. Wêr't fariaasje fan wanddikte essensjeel is, moat de oergong tusken beide stadich wêze.
5. Ferbiningsûntwerp tusken dielen
Gewoanwei moatte wy twa skulpen mei-inoar ferbine. Om in ôfsletten keamer tusken har te foarmjen om de ynterne komponinten te pleatsen (PCB-assemblage as meganisme).
De gewoane soarten ferbining:
1). Snap haken:
Ferbining fan snaphaken wurdt faak brûkt yn lytse en middelgrutte produkten. It karakteristyk is dat snaphaken algemien oan 'e râne fan' e dielen binne ynsteld, en de produktgrutte kin lytser wurde. As it wurdt gearstald, wurdt it direkt sluten sûnder ark te brûken lykas skroevedraaier, ultrasone lasestien en oaren. It neidiel is dat de snaphaken hyltyd yngewikkelder kinne feroarsaakje. De skúfmeganisme en liftermeganisme binne nedich om de ferbining fan snaphaken te realisearjen en de malkosten te ferheegjen.
2). Schroefverbindingen:
Schroefverbindingen is stevich en betrouber. Benammen de skroef + moerfiksaasje is heul betrouber en duorsum, wêrtroch meardere demonstraasjes sûnder skuorren kinne wurde. De skroefferbining is geskikt foar produkten mei grutte skoalkrêft en meardere ûntmanteling. It neidiel is dat de skroefkolom mear romte ynnimt.
3). Befestigingsbazen:
Ferbining foar befestigingsbazen is twa dielen te befestigjen troch de strakke koördinaasje tusken de bazen en de gatten. Dizze manier fan ferbining is net sterk genôch om produkten útinoar te meitsjen. It neidiel is dat de skoalkrêft sil ôfnimme as de tiid fan demontemint tanimt.
4). Ultrasone lassen:
Ultrasone lassen is troch de twa dielen yn 'e ultrasone foarm te pleatsen en it kontaktflak te fusearjen ûnder de aksje fan ultrasone lasmachine. De produktgrutte kin lytser wêze, de ynjeksjefoarm is relatyf ienfâldich, en de ferbining is stevich. It neidiel is it gebrûk fan ultrasone mal en ultrasone lasemasine, de produktgrutte kin net te grut wêze. Nei ûntmanteling kinne de ultrasone dielen net wer brûkt wurde.
6. Underkappen
Undercuts binne items dy't ynterferearje mei it fuortheljen fan beide helten fan 'e mal. Undercuts kinne sawat oeral yn it ûntwerp ferskine. Dizze binne like ûnakseptabel, as net slimmer dan in gebrek oan in konseptwinkel fan 'e kant. Guon undercuts binne lykwols needsaaklik en / as net te foarkommen. Yn dy gefallen, needsaaklik
undercuts wurde produsearre troch glide / bewegende dielen yn 'e mal.
Tink derom dat it meitsjen fan undercuts djoerder is by it produsearjen fan de mal en ta in minimum moat wurde hâlden.
7. Stipe ribben / gussets
Ribben yn plestik diel ferbetterje stivens (relaasje tusken lêst en dielôfwiking) fan it diel en fergruttet styfens. It ferbetteret ek de skimmelfeardigens, om't se de smeltstream yn 'e rjochting fan' e rib haastje.
Ribben wurde pleatst lâns de rjochting fan maksimale spanning en ôfwiking op net-ferskine oerflakken fan it diel. Foarmfoling, krimp en útstjit moatte ek ynfloed hawwe op besluten oer ribpleatsing.
Ribben dy't net oanslute by fertikale muorre moatte net abrupt einigje. Stadige oergong nei nominale muorre moat it risiko foar stresskonsintraasje ferminderje.
Rib - ôfmjittings
Ribben moatte folgjende ôfmjittings hawwe.
Rib dikte moat tusken 0,5 en 0,6 kear nominale wanddikte wêze om sinkmerk te foarkommen.
Ribhichte moat 2,5 oant 3 kear nominale wanddikte wêze.
Rib moat 0,5 oant 1,5-graden trekhoek hawwe om útstjit te fasilitearjen.
Ribbasis moat in straal fan 0,25 oant 0,4 kear nominale wanddikte hawwe.
Ofstân tusken twa ribben moat 2 oant 3 kear (of mear) nominale wanddikte wêze.
8. Radiuste rânen
As twa oerflakken elkoar moetsje, foarmet it in hoeke. Op 'e hoeke nimt wanddikte ta 1,4 kear de nominale wanddikte. Dit resulteart yn differinsjaal krimp en ynmakke spanning en langere koeltiid. Dêrom nimt risiko op mislearring ta yn skerpe hoeken.
Om dit probleem op te lossen moatte de hoeken glêd wurde mei striel. Radius moat ekstern as yntern wurde levere. Nea ynterne skerpe hoeke hawwe, om't it barst befoarderet. Radius moat sa wêze dat se befestigje oan konstante regel fan wanddikte. It hat de foarkar om straal te hawwen fan 0,6 oant 0,75 kear muurdikte by de hoeken. Nea ynterne skerpe hoeke hawwe, om't it barst befoarderet.
9. Skroefbaasûntwerp
Wy brûke altyd skroeven om twa heale gefallen tegearre te befestigjen, of PCBA as oare komponinten op 'e plestik dielen te befestigjen. Dus skroefbazen binne de struktuer foar skroeven yn en fêste dielen.
De skroefbaas is silindrysk fan foarm. De baas kin oan 'e basis keppele wurde mei it memme-diel of it kin oan' e kant wurde keppele. Ferbining oan kant kin resultearje yn dikke seksje plestik, wat net winsklik is, om't it sinkmark kin feroarsaakje en koeltiid kin ferheegje. Dit probleem kin oplost wurde troch baas troch in rib te keppeljen oan 'e sydmuorre lykas werjûn yn' e skets. Baas kin styf wurde makke troch ribben te leverjen.
Skroef wurdt op 'e baas brûkt om in oar diel fêst te meitsjen. D'r binne skroeven foar it foarmjen fan triedden en skroeven foar snijwurk troch de loop. Draadfoarmjende skroeven wurde brûkt op thermoplasten en snijskroeven foar tried wurde brûkt op elastyske thermohardende plestike dielen.
Draadfoarmjende skroeven produsearje froulike triedden op 'e ynterne muorre fan baas troch kâlde stream - plestik wurdt lokaal misfoarme ynstee snijd.
Skroefbaas moat juste ôfmjittings hawwe om te wjerstean tsjin skroefynfoegingskrachten en de lading dy't op 'e skroef yn tsjinst wurdt pleatst.
De grutte fan 'e boarring relatyf oan' e skroef is kritysk foar wjerstân tsjin stripping fan triedden en skroefútdraaie.
Buitendiameter fan baas moat grut genôch wêze om hoepelspanningen te wjerstean trochdat foarming fan tried is.
Boarring hat in bytsje gruttere diameter by yngongspartij foar in koarte lingte. Dit helpt by it lokalisearjen fan skroeven foardat jo ynride. It fermindert ek spanningen oan it iepen ein fan 'e baas.
Polymerfabrikanten jouwe rjochtlinen foar it bepalen fan de dimensje fan baas foar har materialen. Skroeffabrikanten jouwe ek rjochtlinen foar de juste boaregrutte foar de skroef.
Soarch moat wurde nommen om sterke lasferbiningen om 'e skroefboarring yn baas te garandearjen.
Soarch moat wurde nommen om ynmakke stress yn baas te foarkommen, om't it kin mislearje ûnder de agressive omjouwing.
Boarring yn baas moat djipper wêze dan de trieddjipte.
10. Oerflakdekoraasje
Somtiden, om in uterlik fan goed uterlik te krijen, dogge wy faaks spesjale behanneling op it oerflak fan 'e plestik kast.
Sa as: tekstuer, heech glossy, spuitferve, lasergravure, hjitte stampen, galvanisearjen ensafuorthinne. It is needsaaklik om foarôf te rekkenjen by it ûntwerp fan it produkt, om te foarkommen dat de folgjende ferwurking net kin wurde berikt of feroarings fan grutte dy't fan ynfloed binne op produktassemblage.